In the heart of every electronics device, from smartphones to spacecraft, lies a complex network of interconnected components. This intricate web is woven onto a foundation known as a Printed Circuit Board (PCB). While the PCB provides the physical structure and pathways for electrical signals, it’s the process of PCB Assembly that transforms this bare board into a fully functional electronic system.
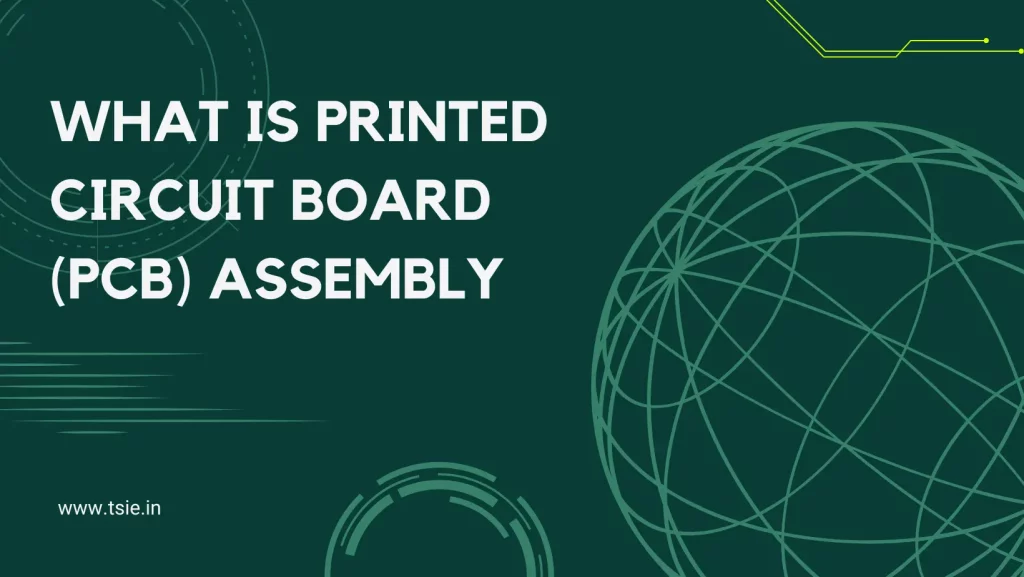
What is a PCB(printed circuit board)?
A PCB, essentially, is a flat insulating board made of materials like fiberglass or ceramic. It’s meticulously etched with copper traces, forming the electrical pathways that connect various electronic components. Think of it as the “brain” of an electronic device, responsible for transmitting signals and controlling the flow of electricity.
What is PCB Assembly?
PCB Assembly is the critical process of attaching electronic components, such as resistors, capacitors, integrated circuits (ICs), and connectors, onto the copper traces of a PCB. This involves a meticulous sequence of steps, ensuring that each component is precisely positioned and soldered in place to create a reliable and functional electronic circuit.
PCBA is a short form for printed circuit board assembly.
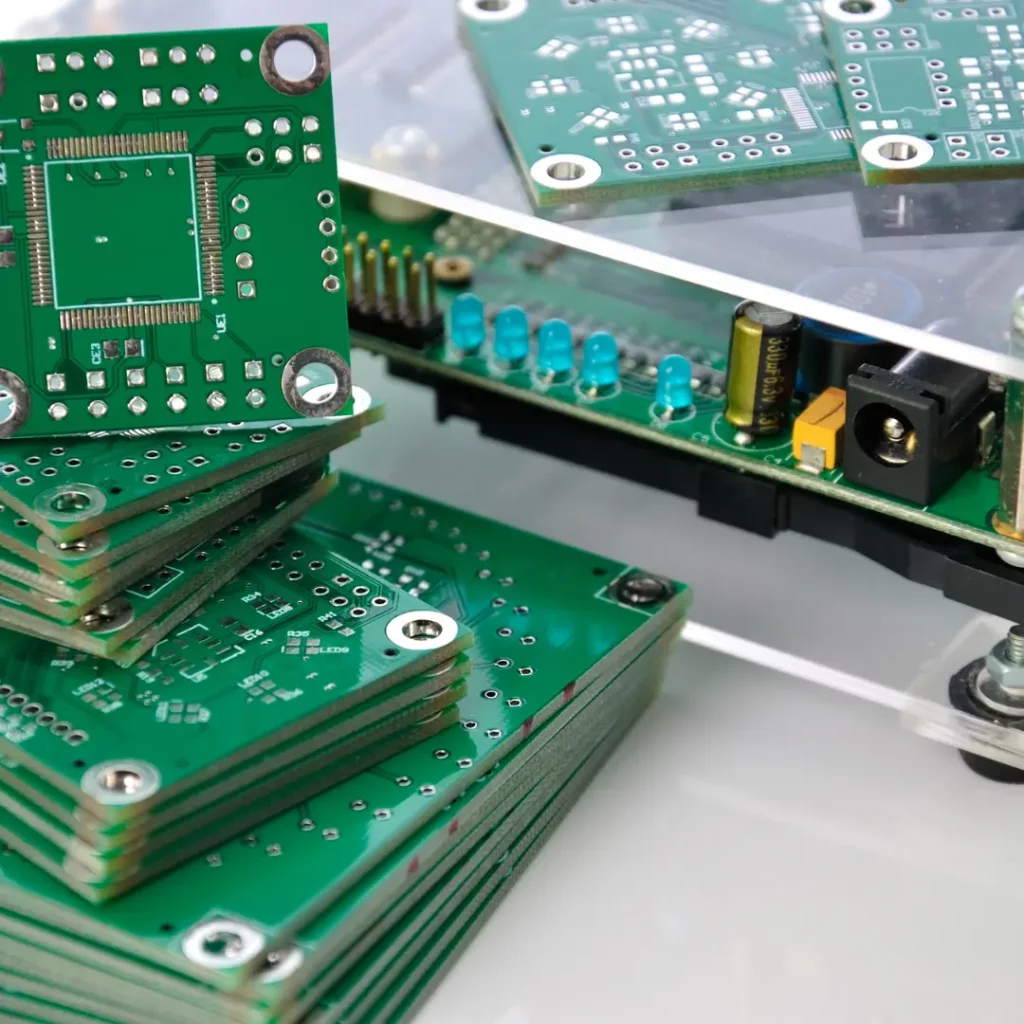
The PCB Assembly Process
The PCB assembly process typically involves the following key stages:
- Design for Assembly (DFA): This crucial initial step involves careful consideration of the PCB’s design to ensure optimal manufacturability. Factors like component placement, accessibility for soldering, and ease of testing are meticulously evaluated to minimize production challenges and costs.
- Stencilling Solder Paste: A stencil, a thin metal sheet with precisely cut apertures, is placed over the PCB. Solder paste, a viscous mixture of metallic alloy powder and flux, is then applied through the stencil openings onto the designated areas where components will be placed. The solder paste acts as a conductive adhesive, facilitating the electrical connection between the component leads and the PCB’s copper traces.
- Placing Components: Automated pick-and-place machines precisely pick up individual components from their respective feeders and accurately place them onto the solder paste on the PCB. These machines can handle a wide range of components, from tiny surface-mount devices (SMDs) to larger through-hole components.
- Reflow Soldering: The PCB, with the placed components, is then passed through a reflow oven. Inside the oven, the temperature is gradually increased, causing the solder paste to melt and flow, creating strong and reliable solder joints between the components and the PCB.
- Quality Inspection: After reflow soldering, the assembled PCB undergoes rigorous quality inspection. Automated optical inspection (AOI) systems are employed to detect any defects, such as missing components, incorrect placements, or poor solder joints. Manual inspection may also be performed to ensure the highest quality standards.
- Functional Testing: Finally, the assembled PCB is subjected to functional testing to verify its electrical performance. This may involve applying various input signals and measuring the output responses to ensure that the circuit operates as intended.
Types of PCB Assembly
- Surface Mount Technology (SMT) Assembly: This is the most common type of PCB assembly, where components are mounted directly onto the surface of the PCB. SMT components are typically smaller and lighter, enabling higher component density and improved circuit performance. Learn more about SMT assembly technology.
- Through-Hole Assembly: In this method, components are inserted into holes drilled through the PCB and soldered from the underside. While less common than SMT, through-hole technology is still used for certain types of components and applications.
Choosing Components for PCB Assembly
Selecting the right components is critical for successful PCB assembly. Factors to consider include:
- Component type: Surface-mount or through-hole, discrete or integrated.
- Size and shape: Compatibility with the PCB’s layout and assembly equipment.
- Power requirements: Ensuring sufficient power supply for the components.
- Environmental considerations: Temperature range, humidity, and other environmental factors.
- Reliability and lifespan: Choosing components that meet the required performance and durability standards.
Advantages of PCB Assembly
Miniaturization: PCB Assembly allows for the integration of a large number of components into a very small space. This miniaturization trend is evident in everything from smartphones to wearable technology.
Compact devices are easier to transport and use in a variety of settings.
Increased functionality: PCBs can accommodate intricate circuits with multiple layers, enabling the creation of highly sophisticated electronic systems with advanced features.
Devices can now perform a wide range of tasks, from simple calculations to complex AI processing, all thanks to the integration of powerful components on a single board.
Improved performance: Facilitates higher speeds, lower power consumption, and better signal integrity.
- Higher Speeds: Precise component placement and optimized signal routing on PCBs minimize signal delays, enabling faster data processing and transmission speeds.
- Lower Power Consumption: Efficient circuit design and the use of advanced components can reduce power consumption, leading to longer battery life and reduced energy costs
- Enhanced Signal Integrity: PCBs provide controlled impedance paths for signals, minimizing signal distortion and ensuring reliable data transfer.
Cost-effectiveness: Automated assembly processes can significantly reduce production costs. PCB assembly relies heavily on automated processes, such as pick-and-place machines and reflow ovens. This automation significantly reduces labor costs and increases production efficiency.
High-volume production of PCBs is cost-effective due to economies of scale and optimized manufacturing processes.
Reliability and consistency: Ensures consistent quality and performance across large production volumes. Rigorous quality control measures, including automated optical inspection and functional testing, ensure the production of high-quality PCBs with minimal defects.
Final Thoughts
PCB Assembly is an indispensable process in the modern electronics industry, transforming bare PCBs into the functional heart of countless devices that shape our daily lives. By understanding the intricacies of this process, from design considerations to rigorous quality control, engineers and designers can optimize their designs, improve product quality, and drive innovation in the ever-evolving world of electronics.
At Tecno System, we excel in PCB Assembly, delivering exceptional quality and reliability. Our expertise spans diverse industries, and we leverage cutting-edge technology and rigorous quality control to ensure precision and efficiency. Experience competitive pricing, fast turnaround times, and a commitment to transforming your vision into reality. Contact us today to explore how we can meet your PCB Assembly needs.
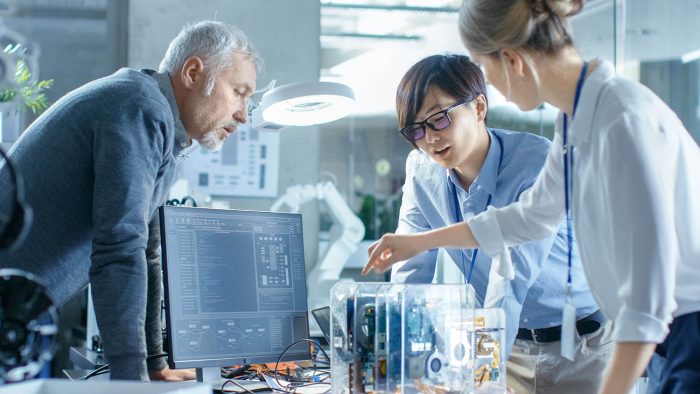
Bring Your Electronics to Life with Tecno System’s PCB Assembly Services
Our expert team and advanced technology ensure high-quality PCB assembly, delivering exceptional performance and reliability
Contact us today for a quote!